Design-Bid-Build is a traditional method of project delivery in which the client contracts with separate entities for both the design and construction of a project. Upon completion of design, the project is typically sent out to bid and usually awarded to the general contractor with the lowest construction costs. When U-SMC is awarded projects, we manage and coordinate all phases from start to finish. U-SMC works diligently by providing greater value to our clients. We self-perform when beneficial to the project and we oversee all subcontractors to control costs and meet our high standards with efficiency and safety.
The Process
Our ability to coordinate and supervise work requirements is enhanced by choosing subcontractors with demonstrated excellent past performance. The first step in our subcontractor selection process is prequalification of those interested in working for us on a contract. The key factors considered in our prequalification process are past performance, safety, experience, economy, and proficiency. During our prequalification process, we also consider the current workload of the subcontractor, available manpower, and specialized areas of expertise. Finally, in prequalifying subcontractors we ask for references from previous completed projects or jobs. U-SMC has an enormous amount of experience managing multiple concurrent projects with a variety of different subcontractor and in-house trades’ personnel involved as well as varying values and scopes.
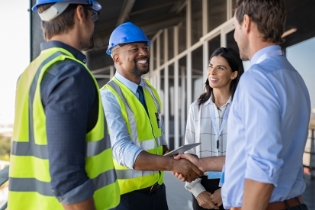
A time-tested process that has been used
almost as long
as construction has been an industry.
U-SMC also has the resources in place to self-perform many scopes, such as interior/exterior architectural finishes, electrical, roofing repair and replacement, facility maintenance and repair, selective and structural demolition, civil and site preparation, and underground utilities. In addition to our our capacity for self-performance, our experienced labor force work side-by-side with subcontractors and contract employees to ensure the highest quality of workmanship our clients expect. A number of our field employees are skilled in multiple disciplines, enabling them to work on several aspects of the same job. For example, a carpenter may double as a concrete finisher, or an electrician doubling as a painter. As a result, even at the field level, U-SMC possesses the proficiency for singular tasks, as well as a broader understanding of how those singular tasks complement each other to complete a complex, multi-disciplinary project.
Our extensive experience allows U-SMC to identify the constraints and risks which might influence an accurate estimate, proposal, and schedule for successful performance. Our systems provide visibility into any potential safety and quality issues. We maintain awareness of regulatory drivers, such as building codes, permitting requirements, design requirements, and environmental impacts. We monitor customer expectations as well as personnel and equipment requirements while entertaining all possible value-engineering and cost-saving options. Our systems accomodate these variations so that efficiency, quality, and order remain at optimal levels. U-SMC considers the safe execution of work our highest priority for our in-house personnel and work performed by our subcontractors. Our approach to the integration of our safety program with our subcontractors promotes a safe and healthy work environment for all personnel. We use a coordinated management approach that allows for accurate cost control, effective scheduling, adherence to safety and quality, and experienced resources that provides consistent, quality construction services.